Published in 2/2021 - Tradition and Renewal
Updating Monomaterial Construction
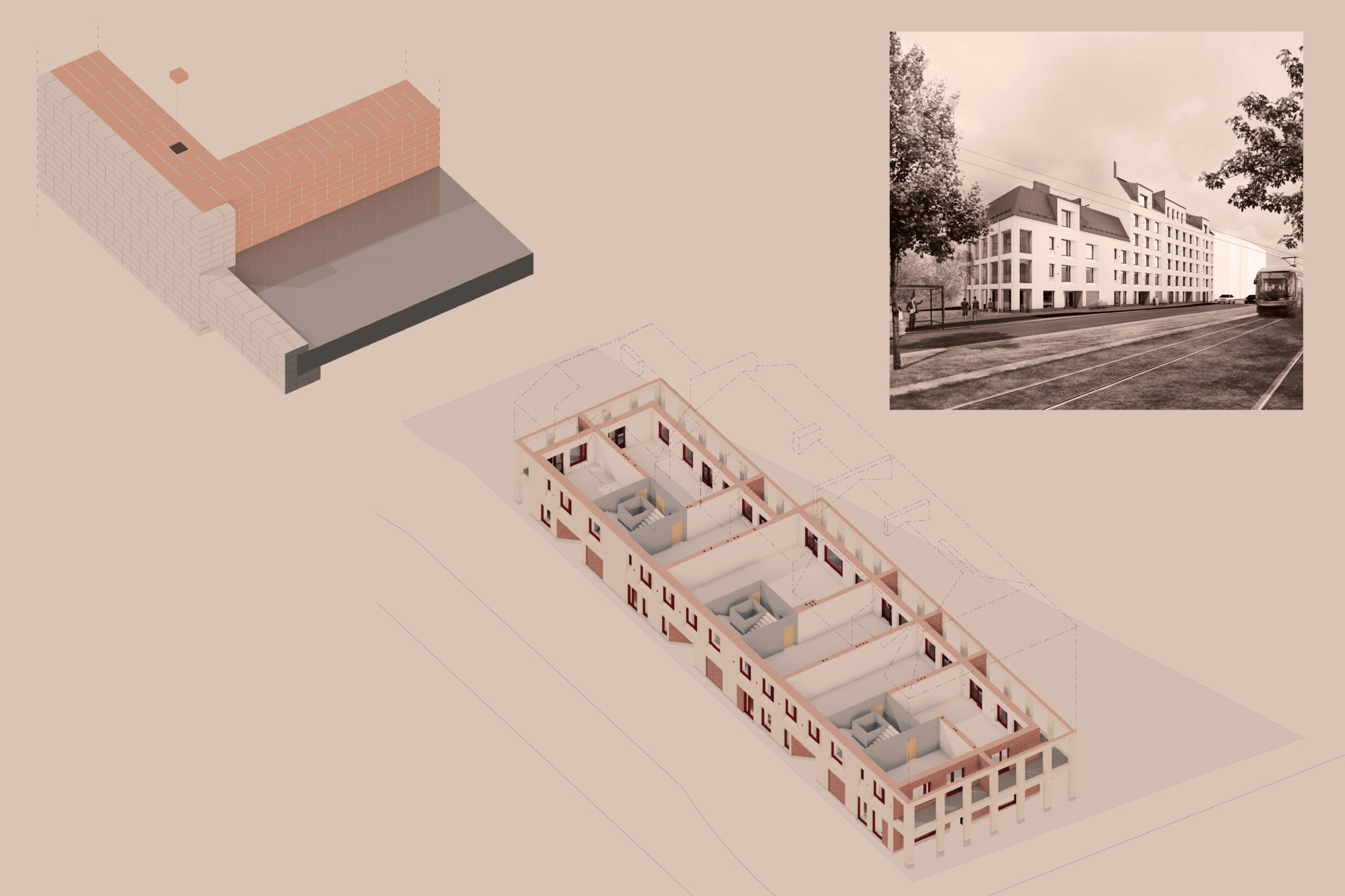
For some time now, there has been talk amongst architects about the return of monomaterial construction. Recently, such buildings, with various scales, have begun to emerge, but there is still a long way to go before this construction method becomes mainstream.
One hundred years ago, almost all building was monomaterial construction, in which one material provided a solution for both the loadbearing capacity and the thermal insulation. For thousands of years, amateur and professional builders alike made everything out of wood, clay and stone. The development of steel and concrete, as well as standardisation, along with industrialisation, opened up new worlds, both structurally and architecturally. Societal phenomena, such as urbanisation, reconstruction and the development of equality, combined with technological development, introduced new kinds of values and objectives to decision makers in the construction field. Cost efficiency, speed and industrial prefabrication became important.
Workers who flooded to cities and towns could quickly be provided with modern housing with facilities. Part of the construction process that was tormented by difficult weather conditions was moved indoors. Light-filled interior spaces and lightweight structures were charming. Valuable construction materials were saved, as more inexpensive materials were now used for thermal insulation and waterproofing. In Finland, the use of multi-layered structures started, and they became a standard of construction in the 1960s. Over the next decade, the calculated thermal insulation requirements became so tight that it was only possible to meet them by using an optimised multi-layered structure. Monomaterial construction was seen as stuffy, extravagant and inefficient, and it was removed from the palette.
Thereafter, the experience gained during the following decades showed that multi-layered structures, which were mathematically optimised to perfection, were not, after all, as perfect as they first appeared to be. Increasing standardisation measures began to narrow down the means of expression and architecture became less versatile. As construction activities became more technical and complex, the understanding of common people regarding construction and their chances to participate in it decreased, and the opportunities of architects to influence matters diminished. The new construction method was taken into use swiftly and extensively, and mistakes were made. There were moisture damages, problems with indoor air quality and buildings that could not be repaired any more. The construction method, which was meant to be perfect, stumbled upon an imperfect world, constructor and user of buildings.
As construction activities became more technical and complex, the understanding of common people regarding construction and their chances to participate in it decreased, and the opportunities of architects to influence matters diminished.
Our perspective on construction has also changed. In recent years, people have begun to pay more attention to the origin of materials, the use of buildings and the time after the use. Our eyes have opened to climate change, loss of species, accumulation of microplastics in the oceans and the decreasing natural resources. A calculated thermal insulation requirement does not tell the whole story of environmental loading caused by a building.
The use of monomaterial building envelopes was almost completely ceased after the mid-20th century and their development came to a halt. Consequently, some of the problems of monomaterial construction – which were dealt with multi-layered structures – still exist. On the other hand, the use of monomaterial envelopes could, for their part, provide solutions for the problems of multi-layered structures. Monomaterial construction is usually linked to adjectives such as environment-friendly, healthy, intelligible, repairable and long-lasting. However, high efficiency and speed are still amongst the priorities in the objectives of the construction field. For instance, the City of Helsinki’s objective for housing construction for 2023 is 8,000 new dwellings a year, whereas in 2009, it was only 1,500 dwellings a year. How could monomaterial construction respond to the challenges faced by present construction activities?
Brick
At least one residential block of flats with a solid brick frame is planned to be built in Helsinki in the next few years. A block of flats designed by Avarrus Architects to be built in Oulunkylä, Helsinki, should receive a building permit in early autumn 2021, as part of the City of Helsinki’s Re-thinking Urban Housing programme. The aim of the programme is to improve the quality of housing, make it more attractive and develop new, distinctive solutions. Recently, a solid brick block of flats was completed in Oulu, designed by Veli Karjalainen Architects.
A solid brick facade was the most common construction method in blocks of flats until the 1960s. According to the principal designer of the building in Oulunkylä, architect Pauli Siponen, we could return to that. “We want to prove that it is still possible to build this way. The goal is to come up with a durable structure which doesn’t need to be serviced and which responds to indoor air problems. Natural ventilation is also an important object of study for us. It interacts pleasantly with a thick, monomaterial external wall”, he explains.
Brick has been used for hundreds of years, and its technical aspects dealing with moisture and heat are known. The brick industry and construction are also part of the Finnish cultural heritage and landscape. However, concrete has replaced brick as the main material in the Finnish construction industry, as it is quick to use and inexpensive. Masonry requires precision, it is labour intensive, and on a current scale, it is slow. A solution to this problem could be provided by robotics. However, it would, at first, be necessary to carry out experimental construction and testing. Siponen says that they have participated in a discussion on a prefabrication of elements for solid brick walls, which could, perhaps, speed up the construction process. However, the block of flats in Oulunkylä will still be masoned on site. The external wall structure consists of a two-brick wall and an outer leaf, chiefly perforated bricks. “The outer leaf will partly be built for aesthetic reasons, but it will also increase the thermal insulation capacity of the building and protect the loadbearing structure from environmental burdens, which leads to a longer lifespan”, Siponen says.
Studies show that solid brick buildings are more energy efficient than what is indicated by calculations.
All means must indeed be taken into use in order to improve the thermal insulation capacity. A solid brick wall cannot meet the thermal insulation requirements placed by the Finnish building regulations, according to which the heat transfer coefficient, or the U-value, may be a maximum of 0.17. However, studies show that solid brick buildings are more energy efficient than what is indicated by calculations. Building regulations do not, for instance, take into account the thermal capacity of materials. As regards the Oulunkylä project, Helsinki Building Control has made an exception, thanks to which the project is allowed to use a less severe limit value, i.e. a thermal insulation requirement (U=0.4) that has been set for mass timber construction. According to Siponen, the U-value of the external walls varies between 0.54 and 0.7. Compensation has been gained by using better insulating windows than normal, as well as from the roof and the base floor. The same reference limit value has been used in the solid brick block of flats in Oulu.
In order to maximise the benefits of the thermal capacity of heavy structures, the building in Oulunkylä will have concrete intermediate floors that are cast on site. This way, heat can be conducted deeper into the frame of the building, reducing temperature variations.
Siponen does not want to recommend just a single material or construction method, but he wants to study different options. “I don’t claim that solid brick and natural ventilation would be the only correct ways to build. In my opinion, monomaterial construction should be increased, but society also has other objectives that cannot necessarily be met with it. Can we tell Helsinki residents that there won’t be more houses as bricks cannot be laid so quickly or trees don’t grow so quickly? Helsinki grows, which must be responded to by the construction field now and in the future.” According to Siponen, multi-layered structures and the materials used in them have improved in recent decades. “The only thing that I oppose is insulated render. A building should feel the same as it looks.”
Honeycomb Blocks
Architect Mikko Summanen from K2S Architects talks about the feel and legibility of buildings when providing grounds for his interest in monomaterial construction. “At our office, we weren’t only fascinated by resource efficiency or a combat against climate change, but also by feelings and the emotional core of architecture. From this starting point, we have moved towards the perspectives of circular economy, life cycle assessment and carbon footprint assessment.”
The opinions and ideals in the construction field have developed in the same direction. Material manufacturers have also sensed the interest in the bringing of monomaterial construction to the new millennium. The brick manufacturer Wienerberger has proposed a solution under the brand name Poroton: clay-based honeycomb blocks with cavities. Many detached houses and schools throughout Finland have been built with it. In the Toritalo building (Jani Prunnila, 2019) in Kotka – the building was nominated for the Finlandia Prize for Architecture in 2020 – honeycomb blocks have also been used, but not as a loadbearing structure.

Monomaterial construction balances between porosity that enables a sufficient thermal insulation capacity and compression strength that is sufficient for loadbearing. Poroton is, by no means, the first or only monomaterial block product on the market. Lightweight concrete, which is better known by the name Siporex, has been used in Finland for dozens of years. However, this porous but fairly weak block has not become a common construction material. In the current, environmentally aware world, a concrete product that has been hardened with aluminium is not attractive, when compared to corresponding products made of natural materials.
In Joensuu, the first Poroton block of flats with six storeys will soon be completed. It is part of an entity formed by three blocks of flats. In the buildings with four and five storeys, Poroton functions as a loadbearing structure, and in the six-storey building, there is an additional support, a composite stanchion in one corner. Mikko Summanen from K2S has been the principal designer of the building. “The building in Joensuu was very easy to construct. In the building, the good aspects of monomaterial construction that has been brought to the new millennium were realised: the building was easy to construct, its building physical qualities are simple and it is fault tolerant. By using half-metre-thick Poroton blocks and a breathable rendering, we will meet the U-value of 0.18”, Summanen explains.
The manufactured materials should be used for as long as possible.
The Poroton block is also available as a version in which the cavities have been filled with perlite, which is a type of volcanic stone. This way, the thermal insulation capacity of a structure can be improved. However, at this point, a question is raised regarding whether this is no longer monomaterial. Summanen reflects on the matter: “In my view, monomaterial construction chiefly deals with single-material structures. However, I wouldn’t define it in such a purist way that I would say that a structure may only contain one material. The main thing is a transfer of moisture through the structure and the levelling of the thermal energy. In my opinion, idealism is needed for the development of matters, but people like us, who are looking for new applications that can be built right now, are also needed.”
Fired clay-based materials are practically everlasting. They are not toxic and they do not harm the environment. However, clay is a non-renewable natural resource, and the firing of clay consumes a great deal of energy. The manufactured materials should be used for as long as possible, by using the buildings for as long as possible and by recycling the materials at the end of their life cycle. The joint is the problem both in traditional bricks and honeycomb blocks. Bricks and blocks could be used for ever, but the currently used strong mortars make demolition much more difficult and the use of a traditional lime-sand mortar is difficult due to both building regulations and the long drying times.
Clay
The use of unfired clay in various forms is one of the oldest construction methods in the world. These kinds of clay structures do not contain any harmful substances and they can be returned to the soil, whilst the manufacture of unfired clay structures does not require much energy. The history of clay construction is also extensive in Finland, but the construction methods have remained at a basic level. The know-how has been in the hands of vernacular builders, but, gradually, more professional use and production have also been studied. The closest place where industrial clay products are available is Estonia, even though in Finland, too, a huge amount of potentially usable clay is transported from worksites to landfills every year.
The architecture studio Collaboratorio is currently studying, together with Vihdin Betoni, opportunities offered by clay and how it could be turned into an industrial product. According to Kristiina Kuusiluoma, architect and partner of Collaboratorio, clay can be used in most of the places where concrete can be used. “There is a vast amount of traditional knowledge, but calculations and certificates are also required in order to introduce clay more extensively to the construction field”, she says. “Solid structures aren’t perfect, but neither were concrete structures when they were taken into use. Opportunities for development work are required.”
Before it is possible to build more with rammed earth, it must be studied and tested for frost resistance, for instance. Kuusiluoma does not regard rammed earth as the best option in Finland for industrially mass-produced external walls. “But, on the other hand, I don’t consider concrete construction to be sensible in this climate, either!”
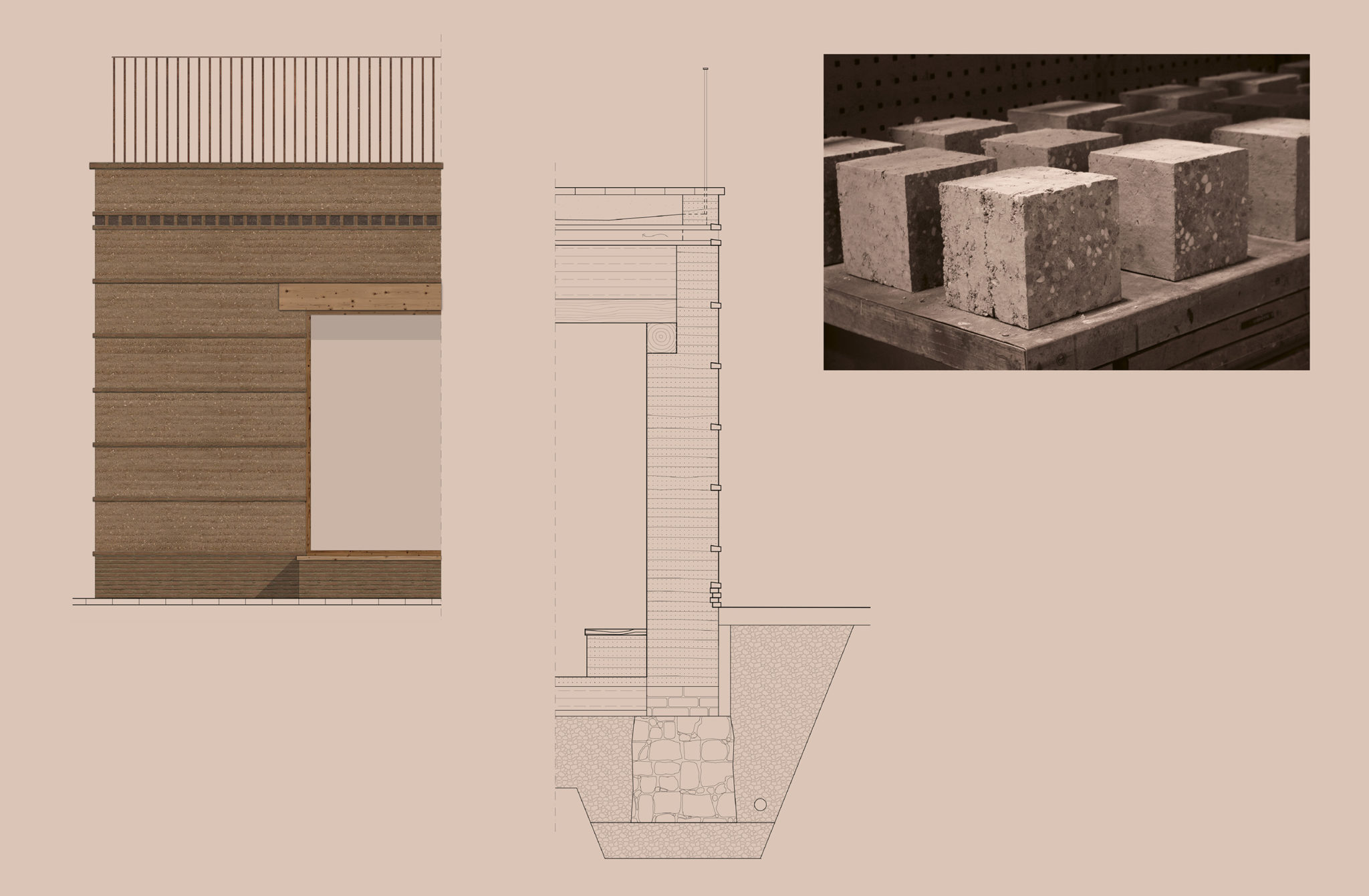
There is a huge pressure on the concrete industry for the development of more ecological applications. If concrete additives are given up, the drying times will be much longer and concrete construction will no longer be financially profitable. According to Kuusiluoma, companies in the concrete industry are very interested in clay construction. “In Finland, there is a good infrastructure and ecosystem for concrete. This ecosystem should be converted to support natural concrete, i.e. clay.”
However, clay has easier uses for which it would be suitable right away. In Finland, a huge number of concrete surface slabs and pump fillers are manufactured for floors. They could be replaced with rammed earth. “The emissions caused by one concrete floor is equal to the construction of 25 rammed earth floors”, Kuusiluoma explains.
”In Finland, there is a good infrastructure and ecosystem for concrete. This ecosystem should be converted to support natural concrete, i.e. clay.”
Like brick, a key quality of clay is its thermal capacity. Kuusiluoma hopes that this would also be taken into account in regulations. “Rammed earth materials could be used, for instance, in public glass-walled lobbies in order to even out the thermal conditions. They could reduce the need for mechanical cooling”, she proposes. In Finland, clay structures have not been observed in building regulations. It would be necessary to create some rules in order to introduce clay more extensively. Germany is the only country in Europe that has norms for clay construction.
Norms are required for construction, and pilot construction is required in order to create norms. Collaboratorio is planning a pilot project in Mäntsälä. A building permit has been granted, but due to the pandemic, the project has been interrupted. In the project that is being carried out with Vihdin Betoni, the drying of various floor structures and the indoor air qualities of clay are looked into. “Clay has outstanding qualities that make the indoor air cleaner. We have found out that clay cleans ozone that is released by copying machines. Ozone is toxic to people”, Kuusiluoma explains.
The potential of clay in construction must be studied further. However, climate change is knocking on the door, and extensive corrective measures must be taken right away. According to Kuusiluoma, a mistake was made in the past when they only began constructing with concrete and forgot the other materials. “Today, we mustn’t make the same mistake and start constructing using only one material. Each material should be in a use that is best suited for it. Currently, the high speed and efficiency of construction using precast concrete panels are best being challenged by the CLT panel technology.”
Wood
Out of monomaterial structures, construction using prefabricated timber elements is currently closest to large-scale industrial production. The increasing popularity has been promoted by projects like the State’s Wood Building Programme. In order to enable wood construction, fire safety regulations have been reformed many times and less strict limit values have been set for thermal insulation requirements than for other construction methods, which is reasonable as long as the calculation of environmental loading focuses on thermal insulation capacity in general. The future roadmap of the Ministry of the Environment regarding the taking into account of the carbon footprint of construction materials will increasingly aknowledge the characteristics of wood. Wood can be produced locally and it is a renewable material that functions as a carbon storage for the entire life cycle of a building. The thermal insulation values of a wood structure are poorer than that of multilayer structures, but when the overall environmental effects of construction are assessed, wood performs well.
Despite the promotion projects and the large media attention, the market share of wood structures in blocks of flats that have more than two storeys is still below one per cent. In detached houses and holiday homes, wood almost has a monopoly. When looking at solid mass timber construction, there are only a handful of pioneer buildings.
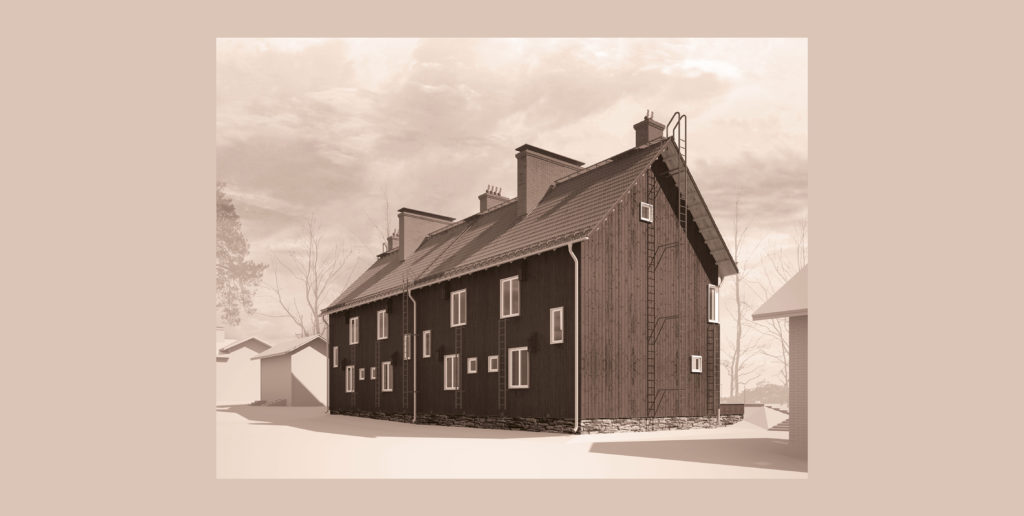
Last year M2-Kodit – which is owned by Y-Foundation – developed, in Jyväskylä, Finland’s first block of flats in which a monomaterial CLT panel, without any separate thermal insulation or cladding, functioned as the external wall structure. In addition to environment-friendly aspects and a good indoor air quality, the idea was also to create a special feel of wood construction in the building. Leaving the wooden surface visible was one key reason for selecting a solid structure. “The aim was to make the exterior architecture resemble a log building”, says Riku Lehtiö, project manager from Y-Foundation. The entity formed by two blocks of flats has been designed by AT Architects. The buildings were constructed by using prefabricated modules that weigh less than concrete elements, which is why their transport from factories to worksites is more energy efficient. In the summer of 2021, an architecturally similar building, with separate thermal insulation, will be completed in Kuopio. The energy consumption of these two blocks of flats will be monitored and compared in the future. In terms of costs, the projects are similar, if the costs dealing with the foundations that were built on different kinds of plots are not observed.
Traditionally, log has been the main building material in Finland. Log construction became less popular after the wars, but it has gradually become more common, first in the construction of detached houses and holiday homes and, in recent years, in the construction of public buildings, particularly schools. The indoor air problems in Finnish school buildings are common knowledge, and it has been proposed that wood construction be one solution for it. Wooden surfaces also improve acoustics and people’s ability to concentrate.
The Pudasjärvi school campus designed by Lukkaroinen Architects – the design received the Wood Award (Puupalkinto) in 2016 – was the largest log building in the world when it was completed. AOR Architects aims at doing even better in Tuusula over the next few years: Monio – a combination of a school and a community centre – is being designed, and when completed, it will be the first three-storey school made of logs. The height will be created by using non-settling laminated logs. Like Pudasjärvi campus, Monio also consists of separate log buildings between which there is tall lobby space. The CLT-structured intermediate floors are carried by glue laminated timber pillars, separate from the log walls. The idea of building with logs was created when sketching the victorious competition entry. “Monomaterial construction is one possible solution for healthier construction and the indoor air problems at schools. We also wanted to propose new aspects to construction”, says Mikki Ristola, partner of AOR Architects.
Even though engineered wood products are marketed as the most environment-friendly solution in the construction field, products with a low degree of processing would also be quite a sustainable alternative. According to Marko Huttunen, architect and partner of Livady Architects, traditional logs are invincible: they have the smallest carbon footprint in the manufacturing phase. Livady recently participated in the Arctic Council’s Zero Arctic project, in which two case study buildings were designed, side by side, for a life cycle assessment. One of the buildings was made by using the CLT technique, the other was built of logs. “Both achieved carbon neutrality, but when looking at an individual construction element, the carbon footprint of a log was much smaller than that of a CLT block. It was also worthwhile building the roof and the base floor from sawn timber. The use of glue laminated timber made the carbon footprint of individual construction elements tenfold”, Huttunen compares.
“I have realised that there is not much other than solid wood that can be recycled.“
There are also other wood products somewhere between carved logs and glue laminated timber products, but they are not yet used extensively. There are already some domestic options. Aalto Haitek’s product is based on components made of wave layered timber. The components are connected by steel bars. This material has been used for townhouses, designed by Livady, by the Huopalahti station in Helsinki. The elements manufactured by Kvarken Massive are connected by using wooden pegs. The benefit of such unglued wood products is that they can be dismantled after their use. Without any adhesive layers, wood can also function hygroscopically freer and hazardous chemicals will not enter either the indoor air during the use of a building or the atmosphere at the beginning and end of its life cycle.
The adhesives used in glue laminated timber are developing constantly. For instance, the development work that is based on lignins in the wood may provide an environment-friendly alternative for the wood construction industry.
Marko Huttunen has worked within renovation for 30 years and has dealt with various materials at the end of their life cycle. “I have realised that there is not much other than solid wood that can be recycled. The frames built of other materials cannot be dismantled in such a way that their degree of processing will not decrease in recycling.” For instance, the demolition of a brick or Poroton block does not necessarily cause a large damage for the environment, but according to Huttunen, their reuse is not currently possible. In his view, multi-layered structures are even poorer. “It isn’t worthwhile repairing or preserving buildings with multi-layered structures. We cannot participate – particularly in the current state that the world is in – in the construction of any more such types of buildings.” ↙
ELINA KOIVISTO is an architect, who teaches architecture and building technology at Aalto University, designs, writes and wonders about how architecture could promote friendly co-living on this unique planet.